More circular projects
Schiphol stimulates new circular economy initiatives. The circular economy is getting more and more attention, but there is still a lot to be done. Schiphol wants to make a contribution and show what the many possibilities are. The knowledge we gain can then be used by other parties. And that’s how we’re going to reach our goal of becoming a completely circular airport by 2050.
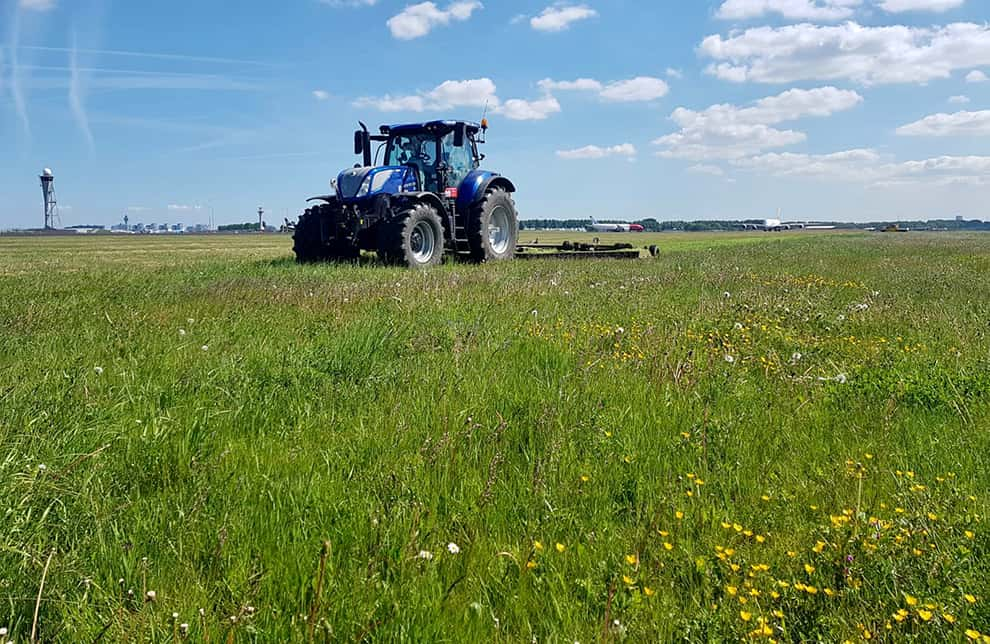
From grass to construction panels
Schiphol is having grass cuttings from the fields around the runways turned into construction panels. This project is the result of a collaboration with ECOR, a company that presses panels from fibres under high pressure. All kinds of fibres can be used for this, including grass fibres. The panels are used to make construction materials, which Schiphol’s construction partners use in a variety of building projects. Once a ceiling panel or partition wall has reached the end of its useful life, it goes back to ECOR. They then reuse it to make new panels, which are then turned into new products.
Floor made out of recycled plastic
2000 m2 of recycled plastic flooring has been laid on Pier G. This floor is not only sustainable, but also an artistic eye-catcher thanks to its subtle lines. The company Aectual made the floor using a special 3D printer. All Aectual floors are made from bio-based or recycled material, and production is waste free and CO2-neutral.
Sustainable flax paint
Rigo, a paint manufacturer in IJmuiden, used flax grown at Schiphol to create a sustainable paint called Aquamarijn. This paint has been used at Schiphol, in the P3 long-stay car park, for example. The flax is grown on an area of wasteland at Schiphol, local windmills do the oil pressing and then Rigo uses the oil to make paint. Waternet and the City of Amsterdam were also involved in this pilot.
Circular baggage conveyor belt
Schiphol’s baggage basement is home to a 110-metre long cradle-to-cradle conveyor belt. Installed in 2011, it was the first in the world. This conveyor belt was designed by a company called Vanderlande and Schiphol provided the opportunity for it to be tested. The Blueveyor was designed to be easily dismantled after reaching the end of its useful life, meaning the various parts can be reused. The Blueveyor is 60% more energy efficient because of the special conveyance method it uses.
Want to see how it works?
From waste water to fertiliser pellets
Phosphorus is one of the world’s natural resources that is running out. Schiphol carried out a pilot to extract magnesium ammonium phosphate (which contains phosphorus) from aircraft waste water. It was used to make struvite fertiliser pellets. These pellets were then spread over a part of the runway area where the soil needed enriching. This project was done in collaboration with water treatment partner Evides Industriewater, Vewin (an association of water utility companies) and research institute KWR.
What we do for sustainability
-
To and from the airport
-
At the airport
-
In the air
-
What can you do for the environment?
-
Sustainable living environment
-
News