Shaping the Future of Cargo Together
What if we told you that it’s possible to reduce truck wait times by 69%-89% at Schiphol? That heavy congestion during peak times could become a thing of the past? As part of her graduate thesis study, Rafaela Vrancken proved it was possible, but it comes with some real challenges. The key is for the entire chain to commit to working on solutions together.
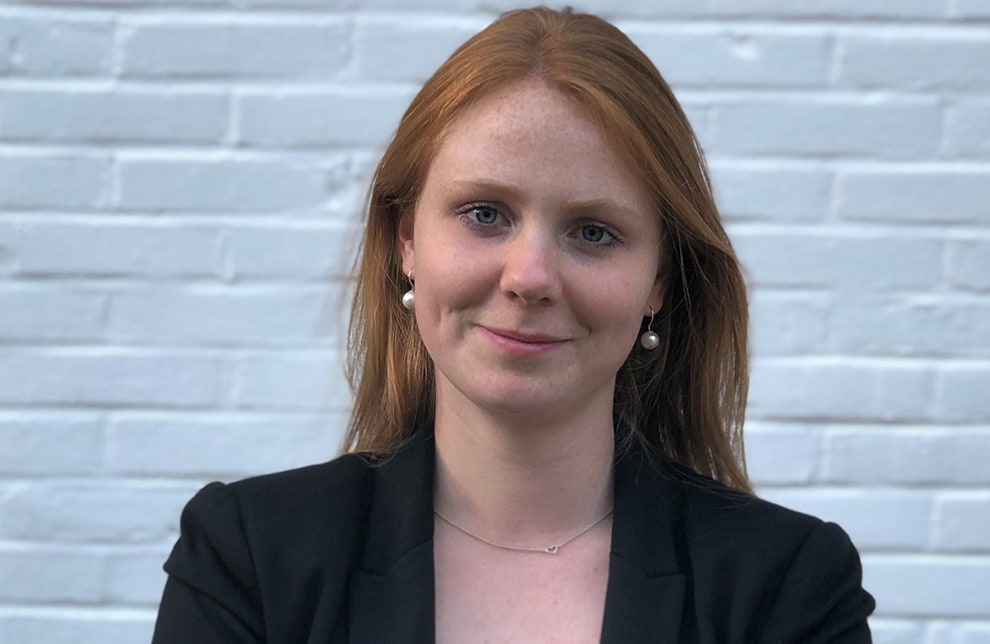
In pursuit of her Master’s degree in Operations Management and Logistics, Rafaela found her passion in exploring the complexities of Transportation & Logistics. What better place, then, than Schiphol’s Cargo division to determine how quantitative studies could uncover efficiency and efficacy improvements.
‘When I started the project, I had this vision that my quantitative analysis would uncover the best ways to reduce wait times and address the congestion that happens when trucks arrive at cargo handlers’ gates at Schiphol during peak times,’ Rafaela explains. ‘But what I discovered is that, given the complexities and the number of stakeholders in the cargo chain, the right solutions are about more than just the numbers.’
The road to less congestion
Rafaela explored five different potential scenarios to implementing a ‘Drop & Collect’ system at Schiphol. That is, a system that allowed trucks to park their trailers in a secure lot until they were ready to be processed. The system would allow for more control of traffic flow, and a just-in-time handling of goods when they are needed for the next stage of transport.
‘Often, a truck arrives at the ground handler with a shipment several hours – or even days – before it is expected to be moved along the chain,’ Rafaela explains. ‘By parking the trailer in a lot, handlers can take care of the trailer or shipments when they need to, instead of when it arrives. In my simulation models, results varied based on the ground handler, the week and the specific scenario. Overall, the models showed that Drop & Collect could lead to a 69%-89% reduction in wait times for the trucks.’
But Rafaela discovered that the solution is not quite that simple. ‘At the moment, there isn’t a single organisation responsible for the entire cargo chain at Schiphol. Ground handlers, transporters and other players are all responsible for their own part, and their own data. But if stakeholders are willing to collaborate more and share their data, the entire cargo chain could be more efficient, and a real win-win situation would emerge.’
A common solution
Rafaela says that significant improvement is only possible when the chain starts working together. ‘And that starts with sharing data. Even the simplest information, like exact arrival times, shipment specifications, (un)loading times and shipment scheduling can provide ground handlers with the insight they need to better organise the flow. When all the reliable data is stored in a single system, the entire chain can benefit.’
Another significant improvement could come from more oversight, she found. ‘My research uncovered as many questions as answers,’ she says. ‘Who is responsible and liable for parked cargo? Who is going to pay? What extra costs come from weekend work? These are all very valid questions that the Cargo community must discuss and agree upon together if they want to make real improvements. Working together for balance and compromise are the key to smoother operations.’
A focus on the future
Rafaela’s primary message to the Cargo community? Vast improvements are possible, if you’re willing to work on them. ‘Every stakeholder in the cargo chain can help reduce wait times and improve the overall process more than they imagine is possible,’ she says. ‘The key is to work together to balance reducing wait times with the other priorities of the chain, and to find a solution that helps each stakeholder equally.’ In short: the future of the Cargo community is in our hands. And by working together, we can find a better way.